In the context of welding, the term ‘consumables’ may sound rather innocent, however, their significance cannot be overstated. Welding consumables are the core of any welding process since they determine the strength, durability, and quality of the welded structures. Here we discuss the significance of welding consumables and connect them to sustainable welding
What are Welding Consumables?
Welding consumables are materials and components used in the welding process and are used up in the process. They are a necessary facet of the welding operation and can be broadly classified into two categories, The typical components of welding consumables include filler metals and fluxes
What are Filler Metals?
Welding consumables, known also as welding rods or welding wire, are materials that are melted during welding to create the welded joint between the base metals to be joined. They come in the form of solid wires, flux-cored wires, and welding rods. The type of base metals to be welded, the welding process that is to be employed, and the required strength of the weld determine the appropriate filler metal to be used
Common types of filler metals include
- Mild Steel Filler Metals : Applied to low carbon steel welding where high tensile strength is not required in the welded structure.
- Stainless Steel Filler Metals : Used in welding stainless steel alloys, which provides good corrosion protection and mechanical characteristics.
- Aluminum Filler Metals : It is used particularly for welding aluminum alloys and offers good strength and ductility.
- Nickel Alloy Filler Metals : Used in welding of high temperature and corrosion resistant materials like Inconel and Monel.
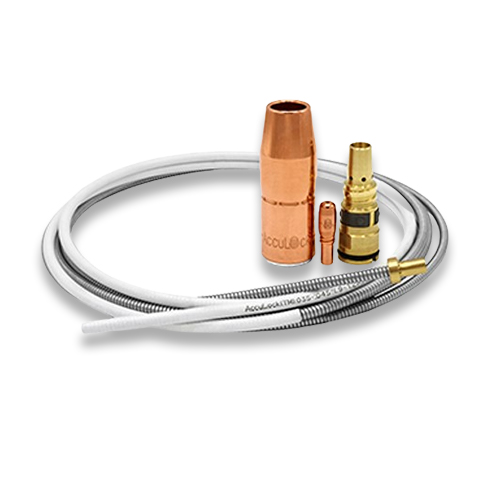
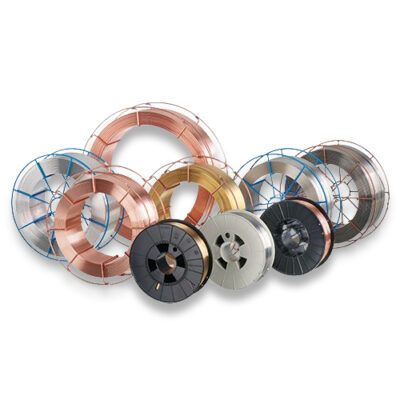
What are Fluxes?
Fluxes are employed to shield the weld pool from the environment and assist in welding. In the form of powders, granules, or coated rods, fluxes are indispensable in protecting the molten weld pool from oxygen and nitrogen to avoid porosity and brittleness by supplying the required amount of reducing gases
Flux Types
- Shielding Gases : In gas metal arc welding (GMAW) and gas tungsten arc welding (GTAW), inert or non-reactive gases like argon or helium shield the molten weld metal from atmospheric contamination.
- Flux-Cored Wires : These wires have a core filled with flux compounds, eliminating the need for external shielding gas. Compared to matching solid wires, flux-cored wires offer increased weld penetration and higher deposition rates.
- Submerged Arc Welding (SAW) Fluxes : SAW fluxes are granular fluxes that form a protective layer on the weld pool, shielding it from the surrounding atmosphere and aiding heat transfer.
Composition and Characteristics
Welding consumables are prepared from materials that are chosen to suit the welding process and the required characteristics of the weld zone. Regarding the filler metals, their composition is usually similar to or similar to the base metal to enable compatibility and efficiency. Fluxes have components that form a shield around the weld pool to allow correct metallurgical reactions to occur. These compounds consist of deoxidizers, slag formers, and beneficial alloying additions to improve the weld and mechanical characteristics
Application in Welding
During welding, welding consumables have several functions. The filler metals are the main material used in joining the base metals, and they determine the strength and soundness of the weld joint as well as its metallurgical characteristics such as hardness, ductility, and corrosion resistance. Fluxes provide a cover to the molten weld pool and enable the formation of a slag layer to eliminate the contaminants in the atmosphere
Selection Criteria
- Base Metal Compatibility : Consumables should be compatible with the base metals to ensure that the fusion and mechanical properties are obtained.
- Welding Process : Welding consumables depend on the type of welding process and the nature of the work that is being done.
- Weld Joint Properties : The properties of the weld joint that are desirable are strength, toughness, and corrosion resistance.
- Environmental Conditions : Consumables are chosen based on environmental conditions such as temperature, humidity, and exposure to corrosive agents.
- Cost and Efficiency : It is also important to note that the performance requirements should be met while keeping the costs and time as low as possible.
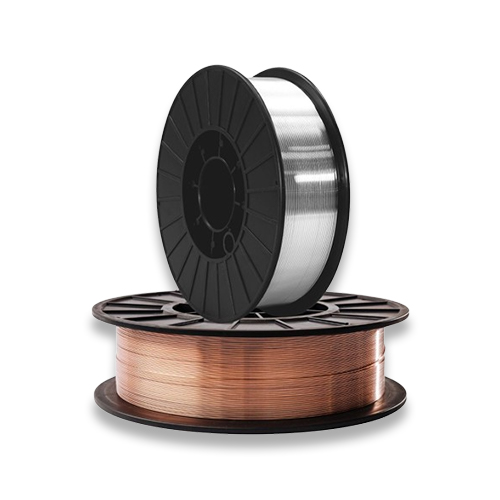
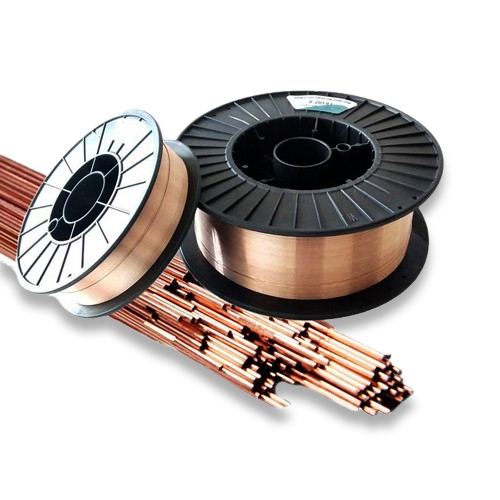
Quality and Performance
Welding consumables play an important role in the quality and performance of the weld joint and therefore should be of high quality. Consumables are tested and certified to meet the quality standards and performance requirements in terms of chemical analysis, mechanical characteristics, weldability, and uniformity. This paper will show that the use of substandard consumables results in weld defects, failures, and safety issues
Compliance with Industry Standards
Welding consumables as the name suggests are used for manufacturing and welding processes, which are also subject to some standards and regulations in terms of safety measures, quality checks, and environmentally friendly usage. Such welding consumables standards are developed by organizations such as the American Welding Society, the International Organization for Standardization, and the European Committee for Standardization. This makes sure that the consumables meet the performance requirements as well as safety measures
Safety Considerations
Safety is paramount in welding operations, and welding consumables pose various safety considerations: Safety is paramount in welding operations, and welding consumables pose various safety considerations
- Hazardous Materials : Some consumables have health risks such as heavy metals and toxic compounds; thus, proper handling is essential to avoid health complications.
- Fume Emissions : Welding consumables produce dangerous fumes and particulates and care should be taken, the necessary cross ventilation, and use of protective covers.
- Fire and Explosion Risks : Flux-cored wires for example can cause sparks and generation of slag and hence if not controlled they can cause fires and explosions.
- Material Handling : The storage and handling of the welding consumables as well as methods of disposal should be properly observed to minimize cases of accidents, spillages, and environmental pollution.
Conclusion
Welding consumables are the backbone of sustainable welding courses; they are crucial to safety, quality, and environmental provisions in welding structures. Welders have a significant part in ensuring the sustainability of manufacturing and construction processes by choosing the appropriate consumables and using and disposing of them properly. The nature of the welding sector is dynamic, and we cannot undermine the role of welding consumables in enhancing sustainability in the processes
Contact Alloyed Sustainables today at sales@alloyedsustainable.com to learn more about our welding consumables and how we can help you in your operations