Powder additive manufacturing or 3D printing has transformed the manufacturing landscape, and the use of powder additives plays a crucial role in achieving sustainable and high-quality production. This blog explores the significance of powder additives in alloyed sustainable manufacturing, highlighting their benefits, applications, and the role of metal powder suppliers for additive manufacturing
What are Powder Additives?
Powder additives are finely powdered materials, often metals or ceramics, that are incorporated into the base material used in additive manufacturing processes. These additives can modify the properties of the final product, enhancing its strength, durability, conductivity, or other desired characteristics
Benefits of Powder Additives in Alloyed Sustainable Manufacturing
Powder additives are revolutionizing the manufacturing landscape by unlocking a myriad of benefits in creating sustainable, high-performance alloys
- Enhanced Material Properties :
Powder additives enable a degree of customization that was previously impossible in traditional manufacturing. By precisely blending different powders, manufacturers can create alloys with specific properties tailored for specific applications. For instance, adding ceramic powders can enhance wear resistance, while metallic powders can improve strength and thermal conductivity. This precise control over material composition results in stronger, lighter, and more durable components, optimizing performance and extending product lifespans. - Reduced Waste :
Additive manufacturing inherently minimizes waste compared to subtractive methods where material is removed from a solid block. Powder additives further amplify this advantage by allowing for the exact amount of material to be used in each build. This precision minimizes scrap and optimizes resource utilization, making it a more environmentally friendly approach. Additionally, unused powder can often be recycled and reintroduced into the manufacturing process, further reducing waste. - Increased Design Freedom :
Powder additives liberate designers from the constraints of traditional manufacturing processes. Complex geometries, intricate internal structures, and lightweight lattice structures are now achievable through additive manufacturing. This newfound design freedom allows for the creation of innovative products with enhanced functionality and optimized performance, unlocking new possibilities in industries like aerospace, automotive, and medical devices. - Sustainable Materials :
Many powder additives can be sourced from recycled or renewable materials, further contributing to the sustainability of the manufacturing process. By utilizing these materials, manufacturers reduce the demand for virgin resources and minimize the environmental impact of production. This closed-loop approach aligns with the principles of circular economy and supports a more sustainable future for manufacturing.
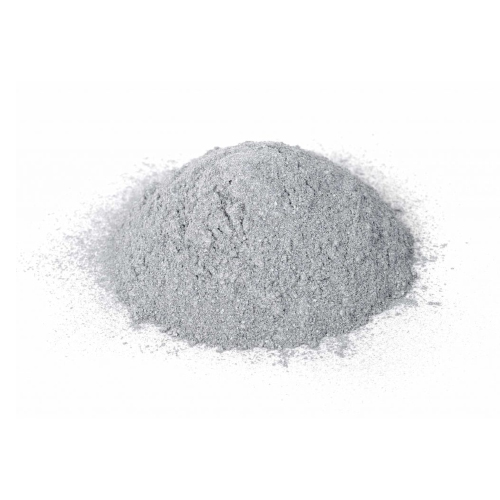
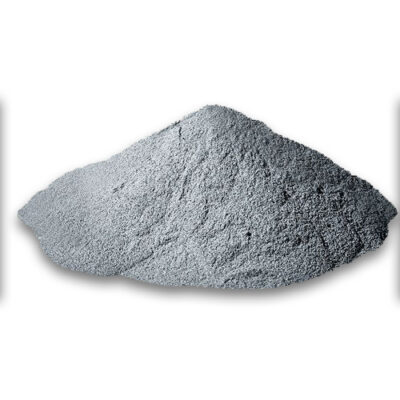
Applications of Powder Additive Manufacturing in Different Manufacturing Processes
Powder Additive Manufacturing (PAM) has revolutionized various manufacturing processes by enabling the creation of complex geometries, customization, and the use of a wide range of materials. Let’s delve into its applications in four key areas :
- Additive Manufacturing (3D Printing) :
PAM is the foundation of many 3D printing technologies. In processes like Selective Laser Sintering (SLS), metal or plastic powders are selectively fused by a laser beam, layer by layer, to create intricate objects. This allows for the fabrication of complex parts with internal structures, impossible to achieve with traditional manufacturing methods. Applications include rapid prototyping, custom tooling, aerospace components, and medical implants. - Metallurgy :
In metallurgy, PAM enables the production of high-performance metal components with exceptional properties. Processes like Direct Metal Laser Sintering (DMLS) and Electron Beam Melting (EBM) use metal powders to create parts with complex internal structures and optimized material properties. This is particularly valuable in aerospace, automotive, and tooling industries, where lightweight, high-strength components are essential. - Plastics and Polymers :
PAM revolutionizes the production of plastic and polymer parts. Selective Laser Sintering (SLS) and Multi Jet Fusion (MJF) use polymer powders to create intricate and durable components. This is used in a wide range of applications, from consumer goods and electronics to automotive parts and medical devices. PAM allows for rapid prototyping, customization, and the production of parts with complex geometries that would be challenging or impossible to manufacture traditionally. - Ceramics :
PAM is also transforming the production of ceramic components. Processes like Stereolithography (SLA) and Digital Light Processing (DLP) use ceramic resins that are cured by light to build intricate ceramic parts. This is particularly valuable in industries like healthcare, electronics, and aerospace, where ceramics’ unique properties, such as heat resistance, biocompatibility, and electrical insulation, are crucial.
The Role of Metal Powder Suppliers for Additive Manufacturing
Metal powder suppliers for powder metal additive manufacturing play a vital role in the industry. They provide a wide range of high-quality powders with consistent properties, ensuring reliable and repeatable results. These suppliers also offer expertise in material selection and process optimization, supporting manufacturers in achieving their desired outcomes
The Future of Powder Additive Manufacturing
The future of powder additive manufacturing is bright. As the technology continues to advance, we can expect to see even more innovative applications and materials. Powder additives will play a critical role in enabling the production of more sustainable, efficient, and customized products across various industries
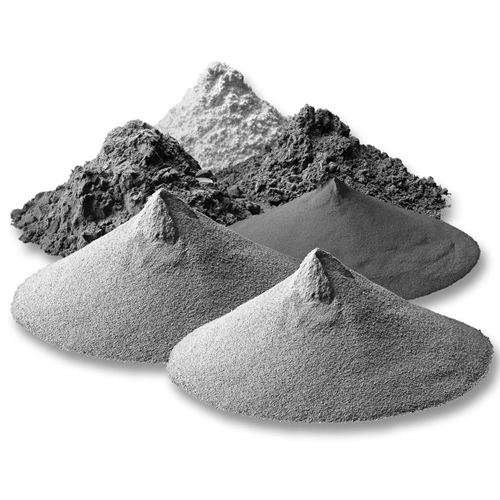
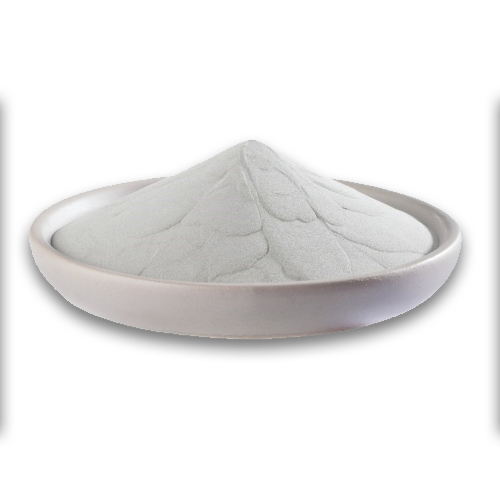
Finding the Right Additive Manufacturing Powder Suppliers
Choosing the right additive manufacturing powder suppliers is essential for success. Look for suppliers with a proven track record, a broad range of materials, and a commitment to quality and sustainability. Several online directories and platforms can help you identify reputable suppliers that meet your specific requirements
In conclusion, powder additives are revolutionizing manufacturing by enabling the production of sustainable, high-performance alloys with enhanced properties. Their role in reducing waste, increasing design freedom, and promoting the use of sustainable materials is invaluable. With the continued support of metal powder suppliers for additive manufacturing, this technology is poised to transform the way we manufacture products in the years to come
Contact us at sales@alloyedsustainable.com to discuss your specific needs and discover how our range of powder additives can elevate your manufacturing capabilities. Together, let’s build a more sustainable and efficient future for your business