Flanges are a critical component in the world of piping systems, connecting pipes, valves, pumps, and other equipment to form a comprehensive flow network. The design, manufacturing, and material selection of flanges require careful consideration to ensure safety, durability, and performance. This article delves into the technical requirements that govern the creation and application of pipe flanges, providing insights into the different flange types and the essential standards that guide their production
Material Selection: The Foundation of Flange Quality
Quality of flanges begins with the conditions of proper selection of materials. The material choice depends entirely on conditions of production, the environment they will be working in, and could include temperatures, pressure, type of transportation fluid. Some of the most common materials to choose are carbon steel, stainless steel, alloy steel, and non-ferrous metals. The properties of each of the materials are unique. Carbon steel is strong and durable. Thus, pressures can reach as much as 100 bars. Stainless steel is great in the sense of being resistant to corrosion, high temperature, and great at welding. It is widely used in food and pharmaceutical industries. Alloy steel is recognized as a superb choice for harsh environments and extreme performance. It can be found in oil and gas and similar industries
Manufacturing Standards: Ensuring Consistency and Safety
There are a number of international standards regarding the manufacturing of flanges that ensure the quality, safety, and compatibility of the manufacturing process. Some of the most popular standards include
- ASME B16.5 : The stated covers pipe flanges and flanged fittings, applicable to sizes from ½ to 24 inches. The principles of the standard cover types of flanges, pressure-temperature ratings, materials, dimensions tolerances, marking, and testing.
- ASME B16.47 : This standard involves flanges that are larger than those in the ASME B16.5. The stated cover large diameter steel flanges and is divided into two types: type A with the sizes at 26 inches and larger and type B which involves flanges at 24 inches and smaller.
- EN 1092-1 : This European standard involves steel flanges and cover these throughout a range of pressure rates, material, and sizes.
- API 6A : This standard is specific to the oil and gas industry and covers flanges fittings used in wellhead and Christmas tree equipment, focusing on materials and performance requirements.
Types of Flanges: A Fit for Every Need
The design and application of flanges fittings are as varied as the industries they serve. The choice of flange types depends on factors like pressure, temperature, and the need for ease of maintenance or assembly. Here are some of the most common types
- Weld Neck Flanges : These are designed to be welded to the pipe, providing a high-strength connection suitable for high-pressure applications. The tapered hub allows for better distribution of stress between the flanges and the pipe.
- Slip-On Flanges : As the name suggests, these flanges are slipped over the pipe and then welded both inside and outside to provide a secure connection. They are easier to align than weld neck flanges and are suitable for lower-pressure applications.
- Blind Flanges : Used to close the ends of piping systems, blind flanges are essential for testing and inspection purposes. They can be custom-made to include openings for pressure testing.
- Socket Weld Flanges : These are used for small-diameter, high-pressure piping systems. The pipe is inserted into the socket end and fillet welded around the top.
- Lap Joint Flanges : Often used with stub ends, these flange types are ideal for systems that require frequent dismantling for inspection or maintenance. They are typically used in low-pressure environments.
- Threaded Flanges : These flanges fittings are threaded to match the pipe, eliminating the need for welding. They are best suited for small pipes in low-pressure systems where welding is not feasible.
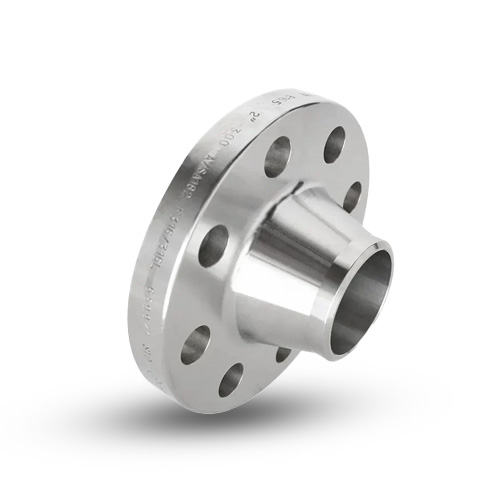
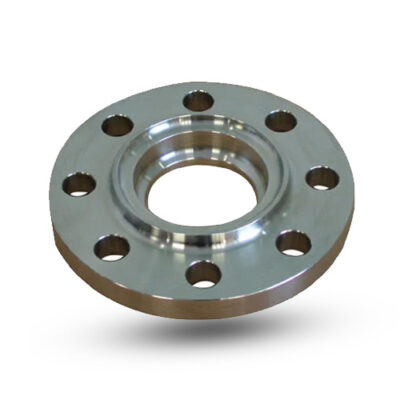
Dimension and Tolerances: Precision is Key
Accurate dimensions and tolerances are critical in the design and manufacturing of flanges. The dimensions must comply with the relevant standards to ensure proper fit and function. Critical dimensions include
- Outside Diameter (OD) : The total width of the flange, crucial for ensuring compatibility with the pipe and other equipment.
- Bolt Circle Diameter (BCD) : The diameter of the circle that passes through the center of the bolt holes, vital for alignment during assembly.
- Thickness : The thickness of the flange plays a significant role in its ability to withstand pressure.
- Hub Diameter and Height : For flange types like the weld neck, the hub’s dimensions must be precise to ensure proper stress distribution.
Surface Finish: Enhancing Sealing Efficiency
The surface finish of a flange is another crucial factor, especially for the sealing surface. A smooth finish ensures better contact with the gasket, leading to a more effective seal. The finish is often measured in micro-inches or micrometers and can vary depending on the application. The most common finishes include
- Smooth Finish : Used in applications where a soft gasket is used, providing a high level of sealing efficiency.
- Serrated Finish : This finish features concentric or spiral grooves that help in gripping the gasket, ideal for high-pressure applications.
- Raised Face : Often found in flanges that are bolted together, the raised face allows for a better seal as the gasket is compressed.
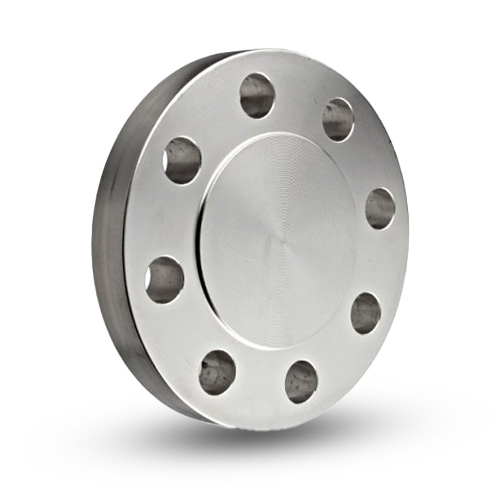
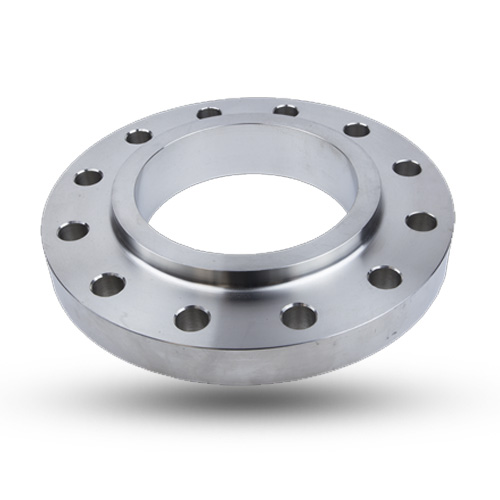
Testing and Quality Assurance: The Final Seal of Approval
Before flanges fittings leave the manufacturing facility, they undergo rigorous testing to ensure they meet the required specifications. Common tests include
- Hydrostatic Testing : This involves filling the flange with water and applying pressure to check for leaks or weaknesses.
- Ultrasonic Testing : This non-destructive test uses high-frequency sound waves to detect any internal flaws or defects.
- Magnetic Particle Testing : Used to detect surface and subsurface discontinuities, this test is essential for ensuring the integrity of the flange.
Conclusion
The technical requirements for flanges are extensive, covering everything from material selection and manufacturing standards to dimension, tolerances, and testing. Each aspect is critical in ensuring that the flanges fittings perform reliably under the demands of various industrial applications. By understanding these requirements, manufacturers can produce pipe flanges that not only meet but exceed industry standards, ensuring safety, efficiency, and longevity in piping systems
You can Contact Alloyed Sustainables today at sales@alloyedsustainable.com to learn more about our Flanges and how they can be uses in various industries.