Grades
categories
Categories
enquire now
WELDNECK FLANGES
Alloyed Sustainables is a Manufacturer, Exporter and Supplier of Raised Face, Flat Face, and Ring Type Joint (RTJ) Flanges that are in accordance with ANSI/ASME B16.5, B16.47, B16.48, DIN, AWWA, and API standards for WeldNeck Flanges. Weld neck flanges are available in the following materials from Alloyed Sustainables: Stainless Steel WeldNeck Flange, Alloy Steel WeldNeck Flange, Carbon and LTCS WeldNeck Flange, Copper & Nickel Alloys WeldNeck Flange, SMO 254 WeldNeck Flange, Nickel WeldNeck Flange, Monel WeldNeck Flange, Inconel WeldNeck Flange, Hastelloy WeldNeck Flange, etc. Weldneck flanges are utilised in many different industries, such as those related to Oil and Gas, Petrochemicals, Pulp and Paper, Pharmaceuticals, Water Treatment Plants, etc.
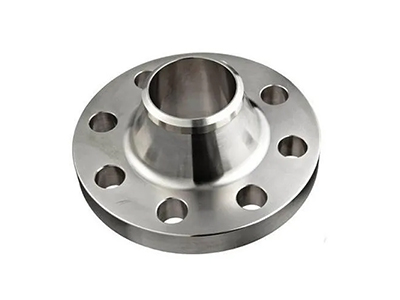
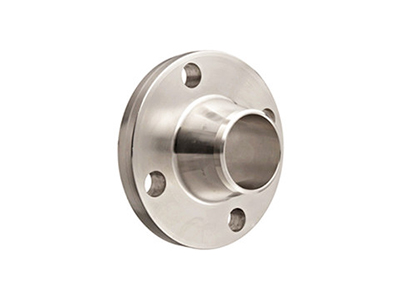
Description:
A Weld Neck Flange is a type of flange used in piping systems to connect pipes, valves, fittings, or other equipment together. Alloyed Sustainables manufactures these flanges in sizes ranging from 1/2″ to 60″. The classes available are 150/300/400/600/900/1500/2500, with a schedule ranging from Sch10 to SchXXS. Weld Neck Flanges are designed to be butted to the pipe. The long tapered hub strengthens the flange, allows for stress relief, and moves the flange face away from the area most impacted by heat. Weld Neck flanges with a conical neck sloping downward from the welding site to the flange are most commonly used in the harshest environments with the most hazardous fluids. It is designed to provide a robust and secure connection between two components while allowing easy access for inspection, cleaning, and maintenance.
Key Features of Weld Neck Flanges:
- Tapered Hub: Long, tapered hub distributes stress evenly and provides a welding point for added joint strength.
- High-Strength Connection: Welded attachment ensures a robust, permanent joint, vital for high-pressure environments.
- Leak Prevention: Flange design combined with gaskets offers effective sealing to minimize leakage risks.
- Bolt Holes: Perimeter bolt holes enable secure fastening to other components or equipment.
- Variety of Materials: Available in diverse materials, suitable for various piping systems and conditions.
- Pressure Ratings: Designed for different pressure levels, making them adaptable to varied applications.
- Easy Welding Access: Extended neck facilitates easy weld accessibility for proper joint formation.
Application across Industries:
- Marine: Vital in shipbuilding and offshore structures for their ability to withstand the corrosive marine environment.
- Power Generation: Essential in power plants for connecting high-temperature and high-pressure pipes, ensuring safety and efficiency.
- Water Treatment: Utilized in water treatment facilities to connect pipes transporting treated water or chemicals, maintaining a reliable flow.
- Chemical Processing: Trusted in chemical plants where corrosive substances flow, thanks to their corrosion-resistant materials and sealing capabilities.
- Oil and Gas: Used in oil refineries, pipelines, and offshore platforms for their durability and sealing properties under high-pressure conditions.
Our dedication to catering to diverse industries is mirrored in our comprehensive range of weld neck flanges, expertly crafted from a variety of materials and grades to precisely match the evolving needs of our clients and industries.
STAINLESS STEEL & DUPLEX STEEL WELD NECK FLANGES:
Specifications:
- Size : 1/2″ NB to 48″ NB, ANSI/ASME B 16.5
- Standard : 150# , 300#, 600#, 900#, 1500#, 2500# in ASA 150 & ASA 300
- Stainless Steel : ASTM A 240 / 182 F – 304/
304H/ 304L/ 316/ 316H/ 316L/ 316Ti/ 309/ 310/ 317L/ 321/ 347/ 904L/Alloy 20 - Duplex steel : ASTM A 182 – F 51, F53, F55
ALLOY STEEL, CARBON STEEL & LTCS WELD NECK FLANGES:
Specifications:
- Size : 1/2″ NB to 48″ NB, ANSI/ASME B16.5
- Class : 150# , 300#, 600#, 900#, 1500#, 2500# in ASA 150 & ASA 300
- Alloy Steel : ASTM A 182 – F5, F9, F11, F12, F22 & F91
- Carbon Steel : ASTM A 105, ASTM A694, F42, F46, F52, F60, F65, F70
- Low Temperature Carbon Steel : A 350 LF2, A 516 GR. 70
COPPER & NICKEL ALLOYS WELD NECK FLANGES:
Specifications:
- Size : 1/2″NB to 6″ NB, ANSI/ASME B 16.5
- Standard : 150# , 300#, 600#, 900#, 1500#, 2500# in ASA 150 & ASA 300
- Copper Nickel : C70600(90: 10). C71500 (70:30), C71640
- Nickel : UNS N02200, N02201
- Monel : UNS N04400
- lnconel : UNS N06600, N06601, N06625, N08800, N08810, N08825
- Hastelloy : UNS N10276, N06022, N10665, N06455
- Titanium Gr: 1,2,3 DTH 3.7025, DTH 3.7035, DTH 3.7055
- SMO 254: UNS S31254
WELDNECK FLANGES
Alloyed Sustainables is a Manufacturer, Exporter and Supplier of Raised Face, Flat Face, and Ring Type Joint (RTJ) Flanges that are in accordance with ANSI/ASME B16.5, B16.47, B16.48, DIN, AWWA, and API standards for Weld Neck Flanges. Weld neck flanges are available in the following materials from Alloyed Sustainables: Stainless Steel Weld Neck Flange, Alloy Steel Weld Neck Flange, Carbon and LTCS Weld Neck Flange, Copper & Nickel Alloys Weld Neck Flange, SMO 254 Weld Neck Flange, Nickel Weld Neck Flange, Monel Weld Neck Flange, Inconel Weld Neck Flange, Hastelloy Weld Neck Flange, etc. Weld neck flanges are utilised in many different industries, such as those related to Oil and Gas, Petrochemicals, Pulp and Paper, Pharmaceuticals, Water Treatment Plants, etc.
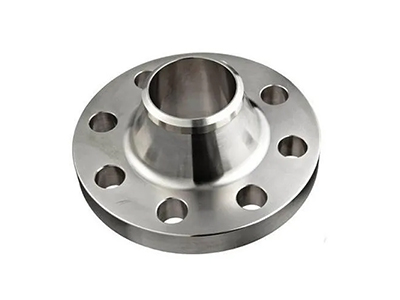
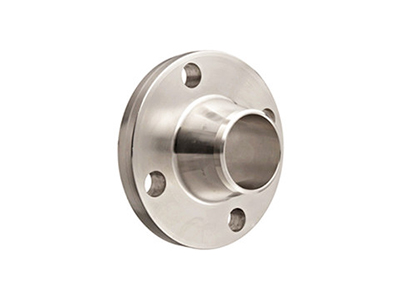
Description:
A Weld Neck Flange is a type of flange used in piping systems to connect pipes, valves, fittings, or other equipment together. Alloyed Sustainables manufactures these flanges in sizes ranging from 1/2″ to 60″. The classes available are 150/300/400/600/900/1500/2500, with a schedule ranging from Sch10 to SchXXS. Weld Neck Flanges are designed to be butted to the pipe. The long tapered hub strengthens the flange, allows for stress relief, and moves the flange face away from the area most impacted by heat. Weld Neck flanges with a conical neck sloping downward from the welding site to the flange are most commonly used in the harshest environments with the most hazardous fluids. It is designed to provide a robust and secure connection between two components while allowing easy access for inspection, cleaning, and maintenance.
Key Features of Weld Neck Flanges:
- Tapered Hub: Long, tapered hub distributes stress evenly and provides a welding point for added joint strength.
- High-Strength Connection: Welded attachment ensures a robust, permanent joint, vital for high-pressure environments.
- Leak Prevention: Flange design combined with gaskets offers effective sealing to minimize leakage risks.
- Bolt Holes: Perimeter bolt holes enable secure fastening to other components or equipment.
- Variety of Materials: Available in diverse materials, suitable for various piping systems and conditions.
- Pressure Ratings: Designed for different pressure levels, making them adaptable to varied applications.
- Easy Welding Access: Extended neck facilitates easy weld accessibility for proper joint formation.
Application across Industries:
- Marine: Vital in shipbuilding and offshore structures for their ability to withstand the corrosive marine environment.
- Power Generation: Essential in power plants for connecting high-temperature and high-pressure pipes, ensuring safety and efficiency.
- Water Treatment: Utilized in water treatment facilities to connect pipes transporting treated water or chemicals, maintaining a reliable flow.
- Chemical Processing: Trusted in chemical plants where corrosive substances flow, thanks to their corrosion-resistant materials and sealing capabilities.
- Oil and Gas: Used in oil refineries, pipelines, and offshore platforms for their durability and sealing properties under high-pressure conditions.
Our dedication to catering to diverse industries is mirrored in our comprehensive range of weld neck flanges, expertly crafted from a variety of materials and grades to precisely match the evolving needs of our clients and industries.
STAINLESS STEEL & DUPLEX STEEL WELD NECK FLANGES:
Specifications:
- Size : 1/2″ NB to 48″ NB, ANSI/ASME B 16.5
- Standard : 150# , 300#, 600#, 900#, 1500#, 2500# in ASA 150 & ASA 300
- Stainless Steel : ASTM A 240 / 182 F – 304/
304H/ 304L/ 316/ 316H/ 316L/ 316Ti/ 309/ 310/ 317L/ 321/ 347/ 904L/Alloy 20 - Duplex steel : ASTM A 182 – F 51, F53, F55
ALLOY STEEL, CARBON STEEL & LTCS WELD NECK FLANGES:
Specifications:
- Size : 1/2″ NB to 48″ NB, ANSI/ASME B16.5
- Class : 150# , 300#, 600#, 900#, 1500#, 2500# in ASA 150 & ASA 300
- Alloy Steel : ASTM A 182 – F5, F9, F11, F12, F22 & F91
- Carbon Steel : ASTM A 105, ASTM A694, F42, F46, F52, F60, F65, F70
- Low Temperature Carbon Steel : A 350 LF2, A 516 GR. 70
COPPER & NICKEL ALLOYS WELD NECK FLANGES:
Specifications:
- Size : 1/2″NB to 6″ NB, ANSI/ASME B 16.5
- Standard : 150# , 300#, 600#, 900#, 1500#, 2500# in ASA 150 & ASA 300
- Copper Nickel : C70600(90: 10). C71500 (70:30), C71640
- Nickel : UNS N02200, N02201
- Monel : UNS N04400
- lnconel : UNS N06600, N06601, N06625, N08800, N08810, N08825
- Hastelloy : UNS N10276, N06022, N10665, N06455
- Titanium Gr: 1,2,3 DTH 3.7025, DTH 3.7035, DTH 3.7055
- SMO 254: UNS S31254